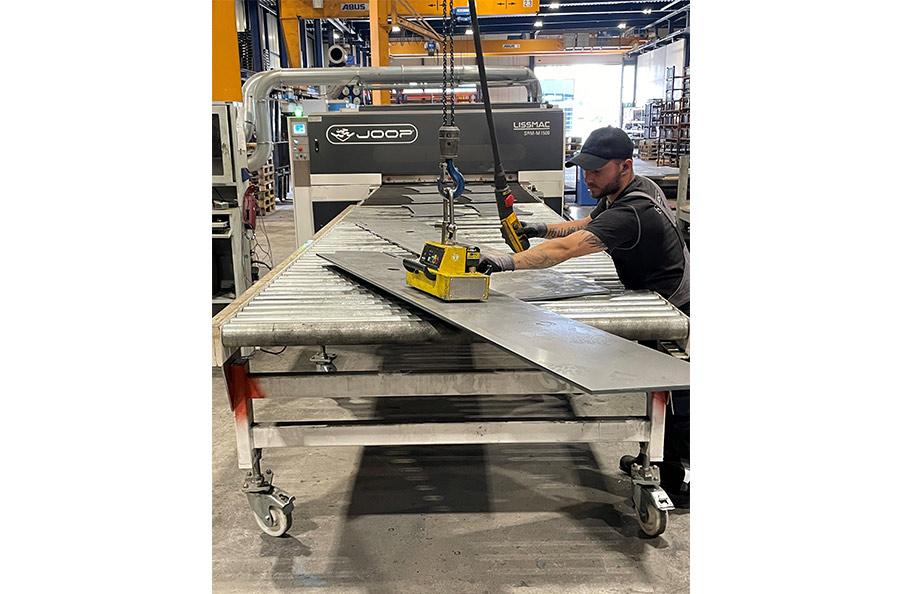
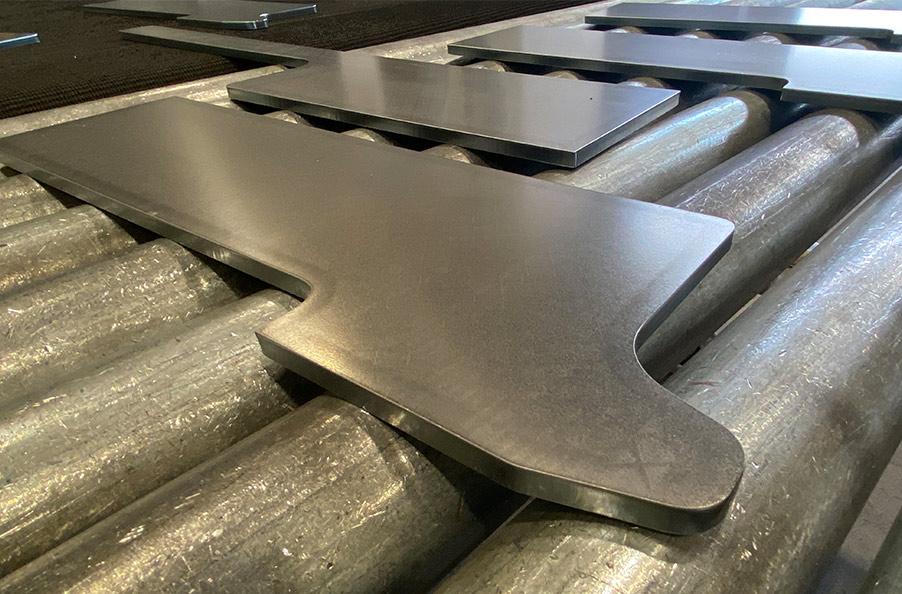
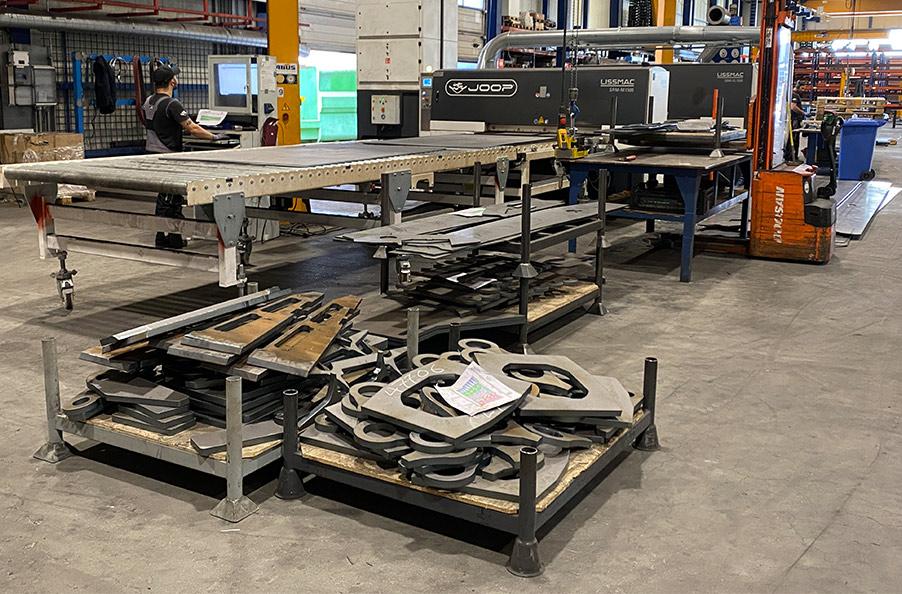
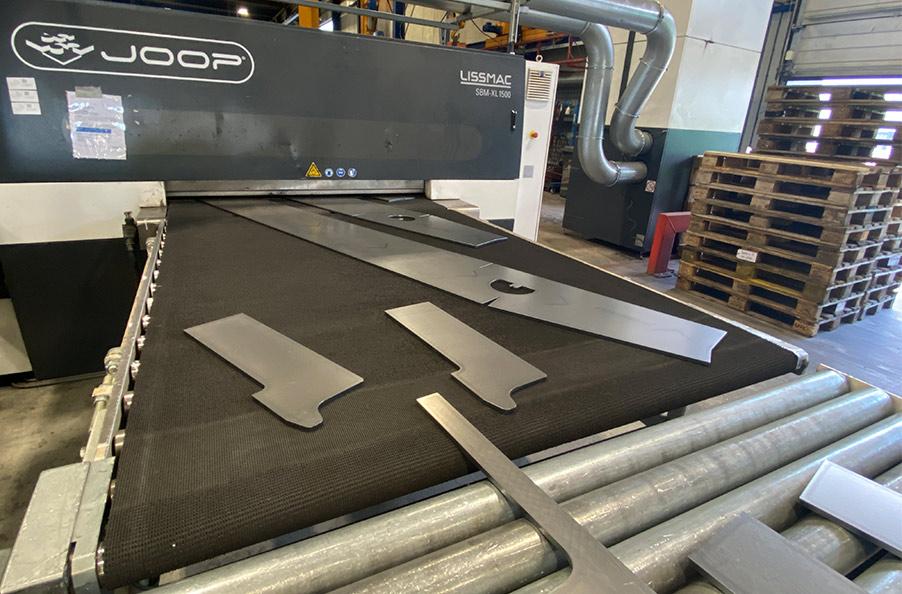
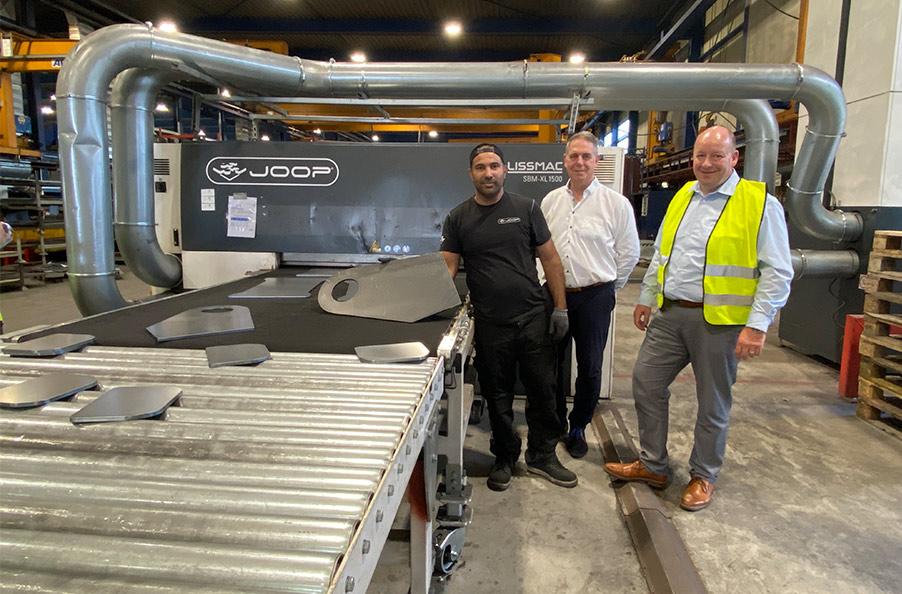
The focus is squarely on automation
November 07, 2024
It always takes visionaries and pioneers to establish something new on the market. A Dutch steel service centre is such a pioneer. Here, the processing of thick sheet metal is to be automated. Two new processing lines from Lissmac that have been purchased are an important building block for this solution.
Text: Annedore Bose-Munde
The family-owned company Joop van Zanten has been a full service provider for plasma and oxy-fuel cutting of steel since 1966. The steel service centre in Veenendaal, Netherlands, now has over 40 employees and processes steel sheets ranging from 2mm to 300mm. It also offers drilling and tapping, folding, straightening, blasting and welding.
Bart Kroesbergen has been plant manager at Joop van Zanten since 2018. He looks back: ‘Six years ago, there was still a lot of manual work at Joop van Zanten. But something had to change, especially in terms of competitiveness, the shortage of skilled workers and the future direction of the company.’ Two questions were on the table from the outset: ‘Can we automate to make work more attractive and more efficient? And above all, can we save costs?’ The steel processor's product range was already very broad in 2018. Therefore, another point was very important: flexibility.
‘The company should be set up for the next 20 years. Increasingly, component manufacturing is being carried out for end producers. To this end, many technologies have been brought in-house, such as welding, machining and edging. We are trying to implement the processes in such a way that they are as automated as possible. This should ensure predictability for new products and product reproducibility, as well as consistent quality and, of course, competitiveness in Europe,’ says Managing Director Kroesbergen, defining the path and goal.
Since 2018, the family-owned company, together with an external director, has implemented a new strategy for the company. At the same time, the next generation of the family are also being prepared for a management position. Together with Bart Kroesbergen, who has an extensive background in business administration, their combined experience, knowledge and shared desire for change has already achieved a great deal. Joop van Zanten is already one of the most modern steel processing companies in the Netherlands, characterised by its high level of automation and digitalisation, and consistently driving forward the topic of Industry 4.0.
Investment in two efficient, identical systems
Joop van Zanten's customer base has changed in recent years. Initially, the company mainly operated as a mass steel cutting company. It was about kilograms and heavy steel. The customers came, for example, from the bridge or shipbuilding industry. But the company wanted to and needed to become more flexible and expand its range of services – including with regard to material thicknesses. Now, the range of processed material thicknesses is in the range of 2mm to 300mm. Currently, the smallest product is a few centimetres in size, while the largest is almost 14 metres. A total of 90,000 different parts were produced in 2023. Today, customers are mostly from industry, mechanical engineering and the transport sector. The focus of production is on supplying customers with a complete end product that has been efficiently manufactured. The processes are to be automated to such an extent that a high level of economic efficiency is achieved.
To achieve these goals, the Dutch company invested in two identical Lissmac systems, each consisting of an SBM-M 1500 D2 slag removal machine, an SBM-XL 1500 G2S2 grinding and deburring machine (passage width of both systems is 1,500 mm), as well as extraction and conveyor technology. The first system was purchased in 2019, the second in 2021.
‘We visited several manufacturers, spoke with system representatives and also looked around at the major trade fairs,’ says Plant Manager Kroesbergen, looking back. But one point ultimately convinced the decision-makers at Joop van Zanten: the two-sided processing that the Lissmac systems make possible. ‘We sometimes run products that are 20 metres long through the systems. The Lissmac technology makes this possible in just a single process step, which makes our work much easier,’ says Kroesbergen. The otherwise necessary handling and the associated complex logistics in the halls are no longer required.
Extensive tests were carried out before the decision was made in favour of the Lissmac Maschinenbau GmbH system. This was also necessary due to the high variety of parts. The practical tests were carried out with the products and materials in mind. Fine adjustments were made and the system went into operation in 2019.
‘We decided that all the parts we manufacture would pass through the Lissmac system. Of course, the surface quality and feel are now better. But every single part also looks really good,’ says Bart Kroesbergen. Based on the technical requirements alone, this would only be necessary for about 50 percent of all parts. But in the meantime, the deburred and rounded parts have also become a quality feature for Joop van Zanten that customers appreciate. And then there is the plant manager's always forward-looking view of fully automated processes. ‘If you have a second processing stream in a process that is not to be automated, it is more difficult to automate it completely.’
The second system, located in a different production area, was purchased in 2021. The production volume had increased significantly, and certain production ranges needed to be processed efficiently for logistical reasons. However, this identical system was also purchased with a view to the planned significant expansion of the automation.
The goal is automation in the thick sheet metal sector
One of the two Lissmac lines will already be used in automated production. Steel sheets up to 40mm thick will be processed here. The second system will be used to process sheets up to 100mm thick. Automation is planned here as well.
‘The requirement that the systems be prepared for future automation was specified by Joop van Zanten at the start of the project for the first system,’ recalls Robert Dimmler, Sales Director Metal Processing at Lissmac. This is also a very important point in terms of ensuring smooth interface communication between different applications and systems.
A system consisting of a slag removal machine, a grinding and deburring machine, and extraction and conveyor technology is one of the machine manufacturer's standard applications. ‘But Joop van Zanten's vision of the automation that was considered from the outset was truly visionary. Automation in the thick sheet metal sector was still uncommon at that time,’ says Dimmler. ’Automation is usually known from the thin sheet metal sector. This was now to be transformed into the thick sheet metal sector, where completely different workpiece dimensions and part weights are common. Being involved in finding a solution here is an exciting part and definitely also a challenge.’
‘Our dream was to use a fully automated factory for thick sheet metal processing within ten years. The question was not ‘will we be able to implement this?’ but rather ‘how will we be able to implement this in concrete terms?’ says Bart Kroesbergen. To this end, experience from other industries was also incorporated into the considerations, for example from concrete construction, where very high unit weights are also involved.
This optimistic thinking outside the box also convinced machine builder Lissmac. ‘A system manufacturer also continues to develop based on customer requirements. And when you have a visionary customer like Joop van Zanten, it also triggers us,’ adds Robert Dimmler. When it comes to new implementation ideas, it's simply part of the process to think outside the box.
The challenge lies in the weight and variety of the parts
The weight, variety and complexity of the structures require new approaches to implementation with regard to automation. The mechanical removal of parts using robotics is therefore not yet fully implemented. Here, Joop van Zanten is working together with Messer Cutting Systems GmbH, Beuting Metalltechnik GmbH & Co. KG and Lissmac on a suitable solution. The goal that the partners involved are working on is a solution that will cover the company's range of thick sheet metal core parts. The systems are to run automatically next year.
The fact that all systems in operation at the Dutch steel service centre are connected to a software platform and OPC UA interfaces is another important point for seamless automation. Machine manufacturer Lissmac has also defined the OPC UA standard (standard for secure, cross-vendor networking for industrial systems) as the standard for its own products.
One example shows how important this topic is: a customer of Joop van Zanten manufactures the frame of a system that produces chips. The steel plates required for this, which are manufactured by the steel service centre, must not be touched by hand so that finger grease does not get onto the systems. Without automation, this would be inconceivable.
One thing is certain: the project partners are working together on a truly visionary task. However, solving this task involves very pragmatic issues: technical implementation, constant communication, and continuous learning and support from each other.