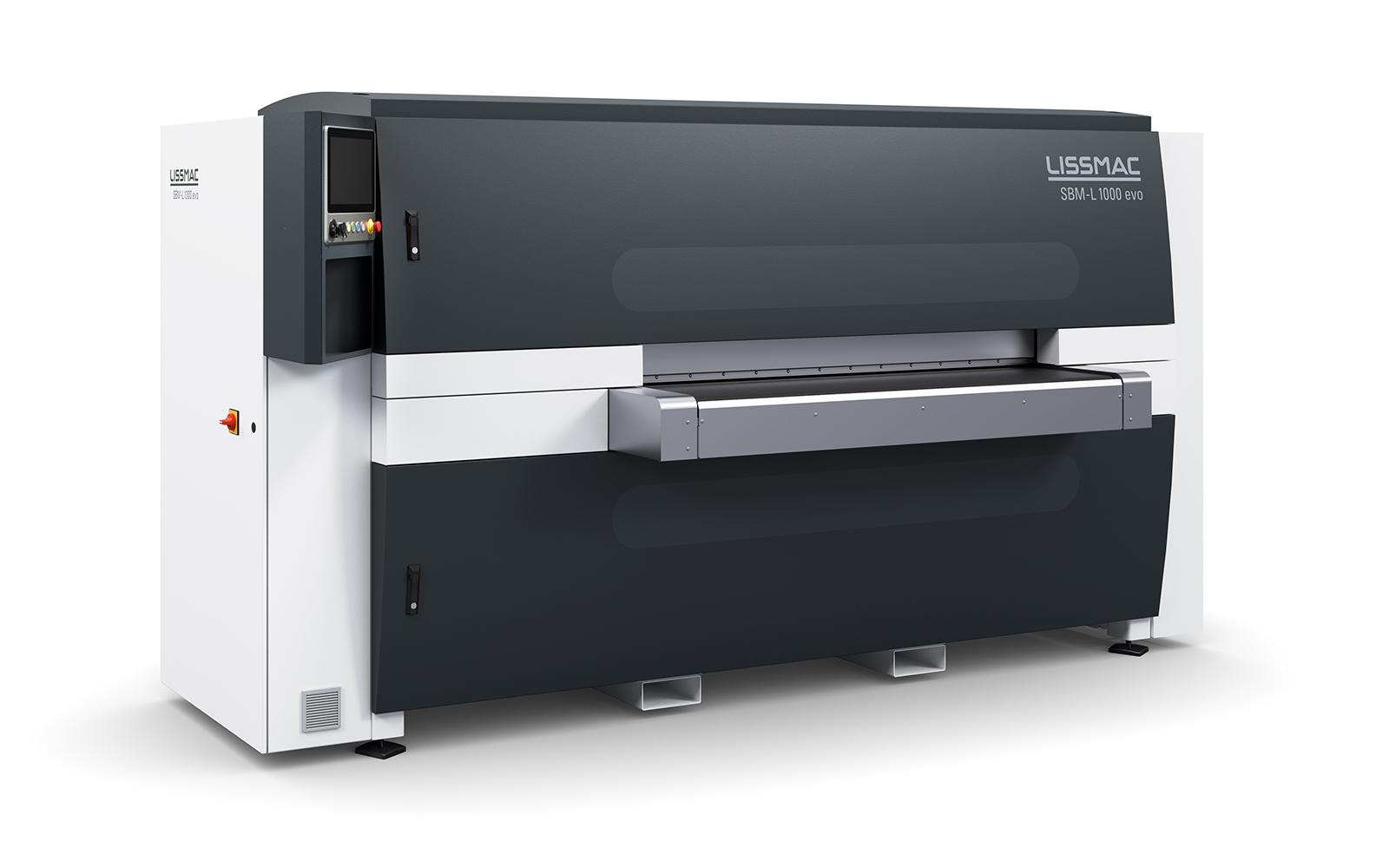
Lissmac automatise la technique de ponçage et d'ébavurage avec ses partenaires
octobre 08, 2024
Automated processes ensure efficiency in sheet metal processing. Take, for example, the automated ejection unit that Lissmac Maschinenbau GmbH is presenting at Euroblech. It is used to separate laser components that are attached to micro bars on the sheet metal panel. Four separately controllable gripper units equipped with a vacuum suction cup selectively remove the laser components from the scrap grid after the micro-bars have been separated by the ejection process. The components are then placed on a conveyor belt for the next process steps - deburring and edge rounding. The system does not require optical image processing as it is based on the geometry data of the cutting plan and automatically determines the required number of suction pads. It can be flexibly adapted for different sheet sizes and thicknesses. The possible component sizes in the current system version range from DIN A5 to Euro pallet format. Sheets with thicknesses from 1 mm to 8 mm and a maximum weight of 90 kg can be processed. Time-consuming manual clearing is no longer necessary. The process is decoupled from laser cutting thanks to a buffer space in the warehouse. The ejection unit can be retrofitted to existing cutting systems or high racks and can be used regardless of the manufacturer.
The automation unit, which the Bad Wurzach-based machine manufacturer developed together with J. Schmalz GmbH, automates the loading of Lissmac grinding machines. The cell relies on robotics technology as well as AI software and 3D vision sensors from the automation technology manufacturer. The components are identified with the help of visual 3D component recognition from Schmalz in order to pick up unmixed components from a pallet. They are then placed on a conveyor belt using a matrix gripper. They can then be deburred in the next process step.
The combination of loading robots with the vacuum grippers from Schmalz and the connection to the sanding system ensures more efficient production processes: Manual loading is reduced so that a deburring machine can be operated by a single person.
The SBM-L Evo series will also be presented as a pre-series model for the first time at Euroblech. On show will be the SBM-L 1000 G1S2 Evo - a deburring machine for deburring and edge rounding on both sides of punched, laser-cut and fine plasma-cut sheets in a single work step. The new top model of Lissmac's double-sided deburring machines has been available as a series machine since April 2024
From the Lissmac product range of single-sided and double-sided grinding and deburring machines for thin and thick sheet metal processing, the SBM-L 1500 G1S2 for highly efficient double-sided deburring and edge rounding of punched, laser or HD plasma-cut parts and the SMD 35 REER (S-Edition) for uniform edge rounding on all edges up to a radius of 2 mm as well as for a non-directional finish and small parts and thin sheet metal processing will also be on show in Hanover. The SMD 123 RE will also be presented, which can be used for deburring and uniform edge rounding on all edges as well as for surface processing of workpieces made of steel, stainless steel and aluminum. Also on show will be the SBM- XS 300 G1E1 Alu Mix for deburring and even edge rounding of small parts in a single operation.
Visitors are cordially invited to the Lissmac stand, Hall 14, Stand 14-K06, to find out more about proven technologies and the new features for Industry 4.0.