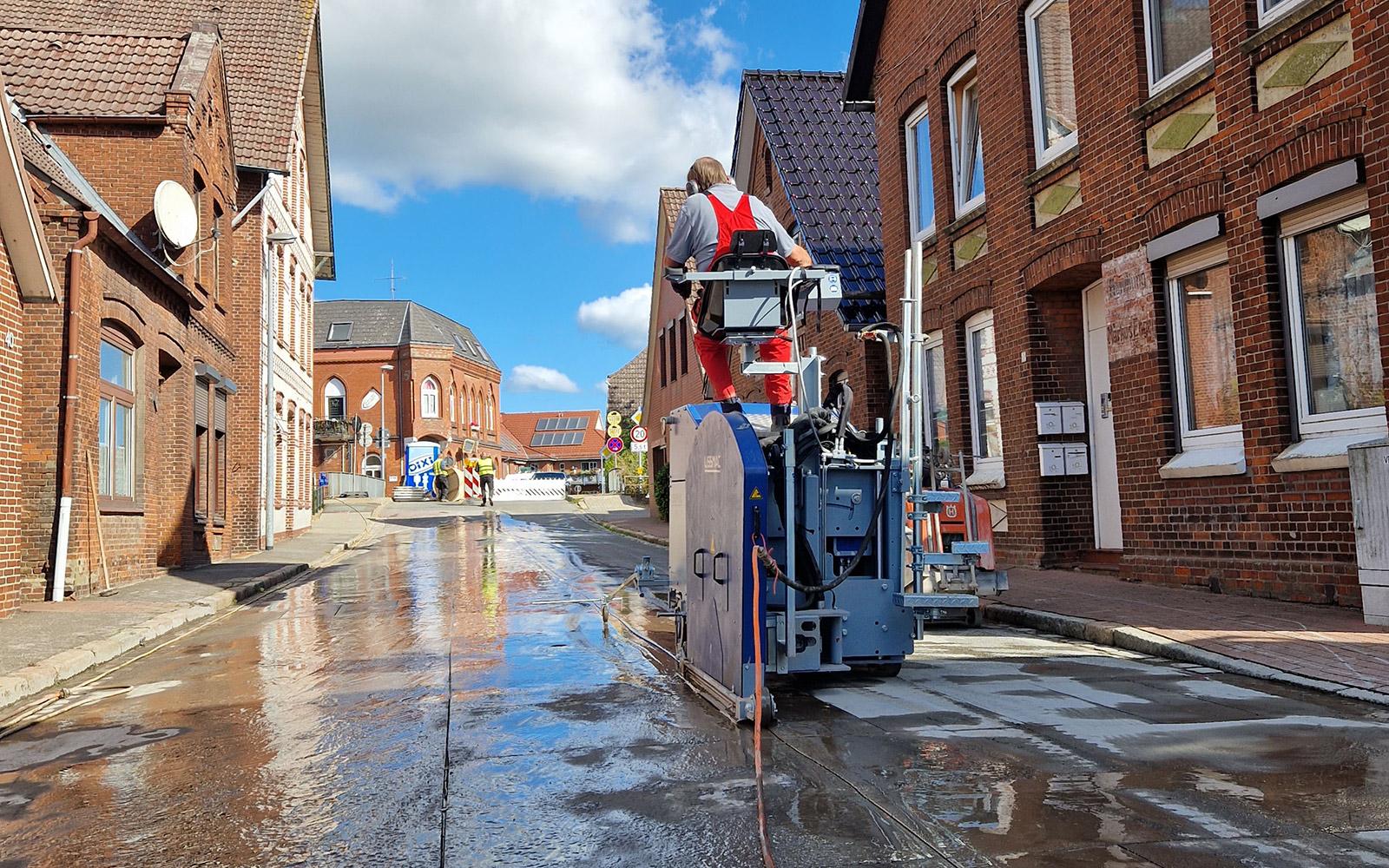
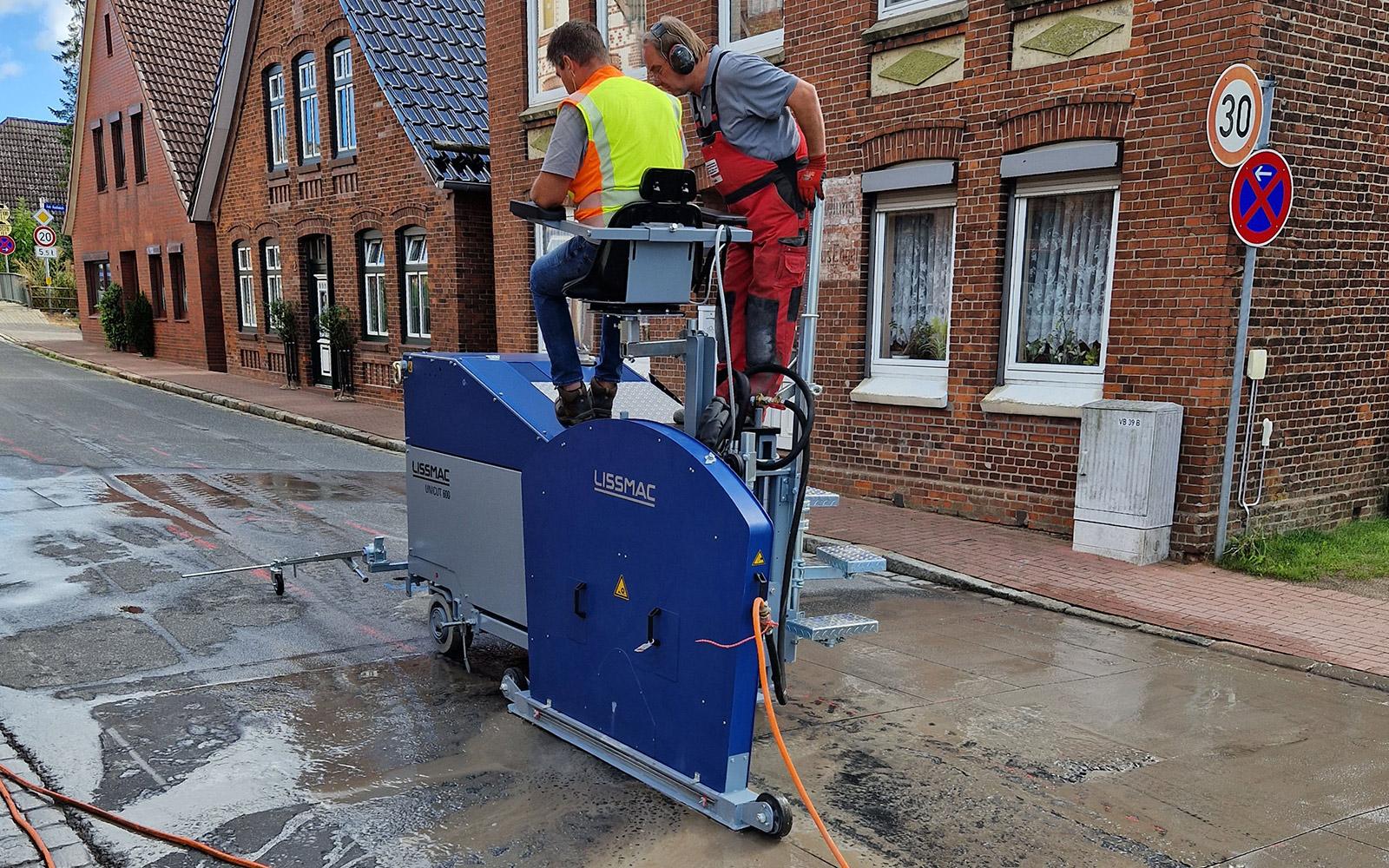
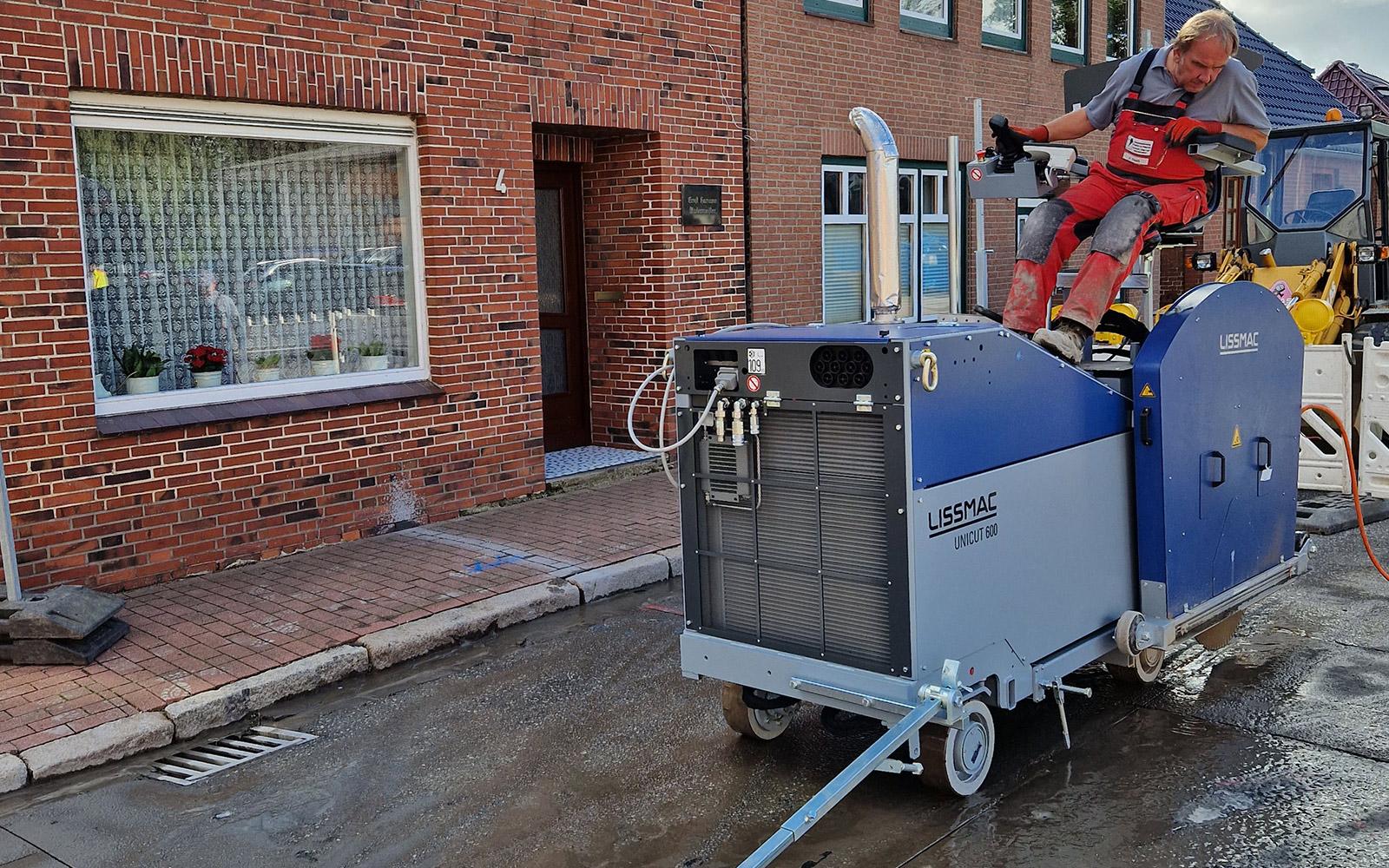
Asphalt Paving In A Sensitive Environment
Februari 08, 2023
LISSMAC UNICUT 600 cuts through 50 cm thick asphalt and concrete
The ground must not shake. This was the premise of the contract awarded by the Friedrich W. Petersen company from Seedorf, which involved the vibration-free removal of a 50 cm thick road surface. Measuring devices in the adjacent houses checked strict compliance with the specification. Cruel methods such as hammering or milling with coarse tools were ruled out. The UNICUT 600, LISSMAC's flagship floor saw, whose diamond saw blade cuts asphalt and concrete surfaces to a depth of up to 63 cm, provided the elegant and efficient solution.
The delicate task took the experts for diamond drilling and sawing technology from the company Friedrich W. Petersen into a narrow residential street. The machines had to come within arm's length of the house fronts in order to remove the massive soil structure in the Aubrücke area in Wilster. Years ago, the marshy subsoil had been filled with concrete during a road renovation to secure the floodplain crossing. "As part of a new house supply, the 50 cm thick layer of concrete and asphalt had to be removed. It was imperative that the work be carried out without vibration. This was documented with measuring devices on the surrounding houses for evidence," reports managing director Willi Petersen, whose company specialises in asphalt and concrete sawing. He was commissioned by the construction company Gerd Dallmeier from Bekmünde to cut the asphalt-concrete mix, once designed for maximum stability, into small pieces that could be gently lifted and transported away with a mini-excavator.
The chessboard-like cut lines, which crossed the resistant floor structure of the Aubrücke bridge to a depth of 50 cm, added up to around 300 running metres. A demanding task for man and machine, which Petersen and his specialists completed quickly and at the same time as gently as possible with know-how and the right equipment. "Such construction measures are naturally a burden for the residents. Keeping this as low and short as possible was a major concern for us. The measurement data from the vibration sensors also confirm that we have achieved this goal," says Petersen. A total of 50 cross-sections were also created, which were drilled off at the sides, in order to render vibration-intensive chiselling out of the cut surface superfluous.
The main load of the cutting work was shouldered by the LISSMAC floor saw UNICUT 600, which is designed for the toughest applications. Travel drive and saw blade speed are electro-hydraulically adjustable. The hydraulically controlled drive proves to be extremely robust even in the toughest continuous operation, can be operated without restriction under full load and works without any appreciable wear. A 100 kW/136 hp Perkins diesel engine provides the power, accelerating up to 1,500 mm diamond saw blades to the set speed and powerfully dragging them across. A highlight from the operator's point of view is the LISSMAC-typical, first-class ergonomics of the machine, which enables low-fatigue floor cutting over many hours. The control is millimetre-precise and effortlessly simple via joystick. The userfriendly design allows multiple seating positions and provides the best overview in both push and drag cutting mode. "The UNICUT 600 makes our back-breaking job much easier. It is fast, precise, reliable and you have a firm grip on the over two-tonne powerhouse with just one finger on the joystick. Every morning, my employees like to get back on the machine. That is good for motivation and it is reflected in our first-class work," says Petersen.
Get more information about the product here.