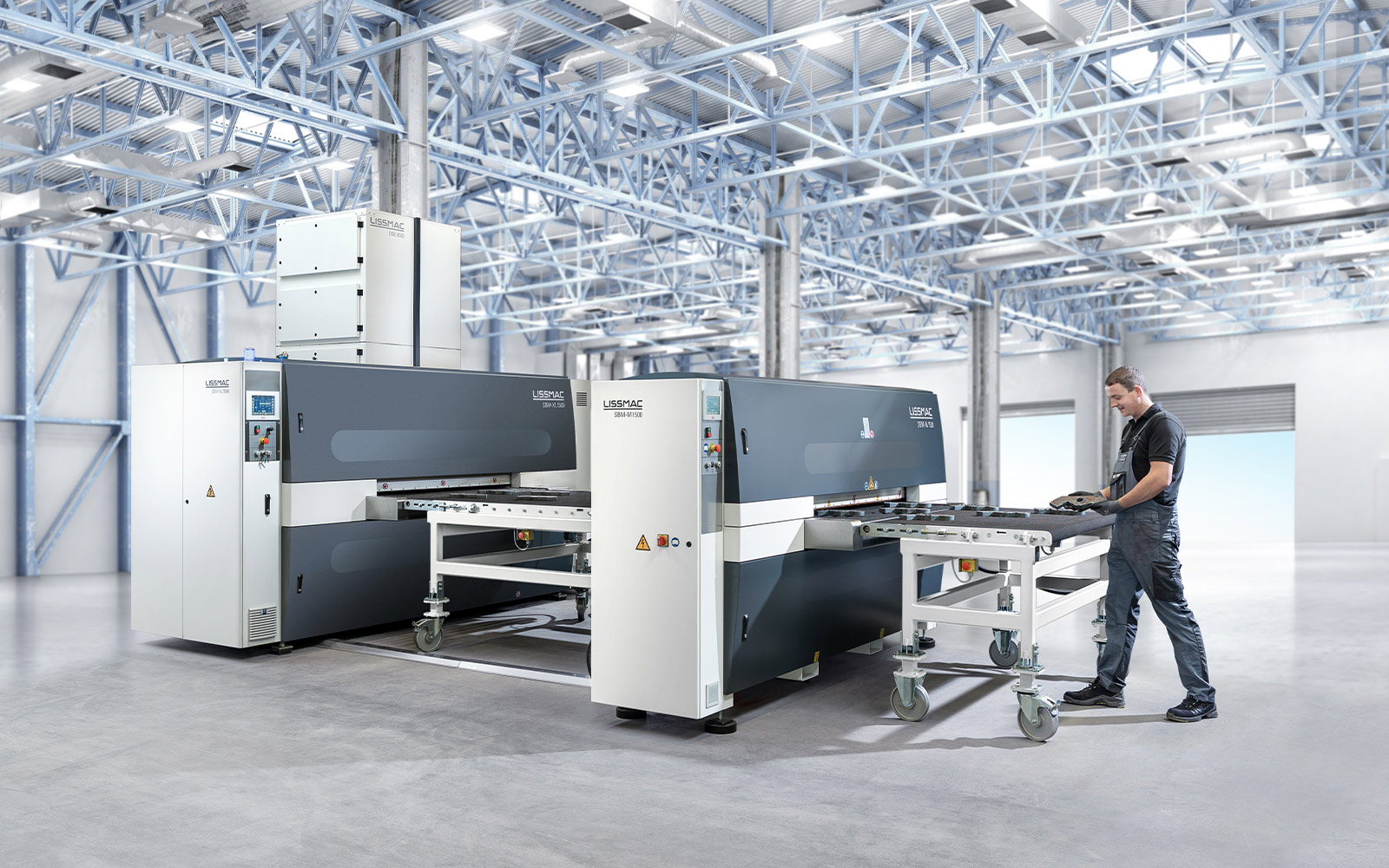
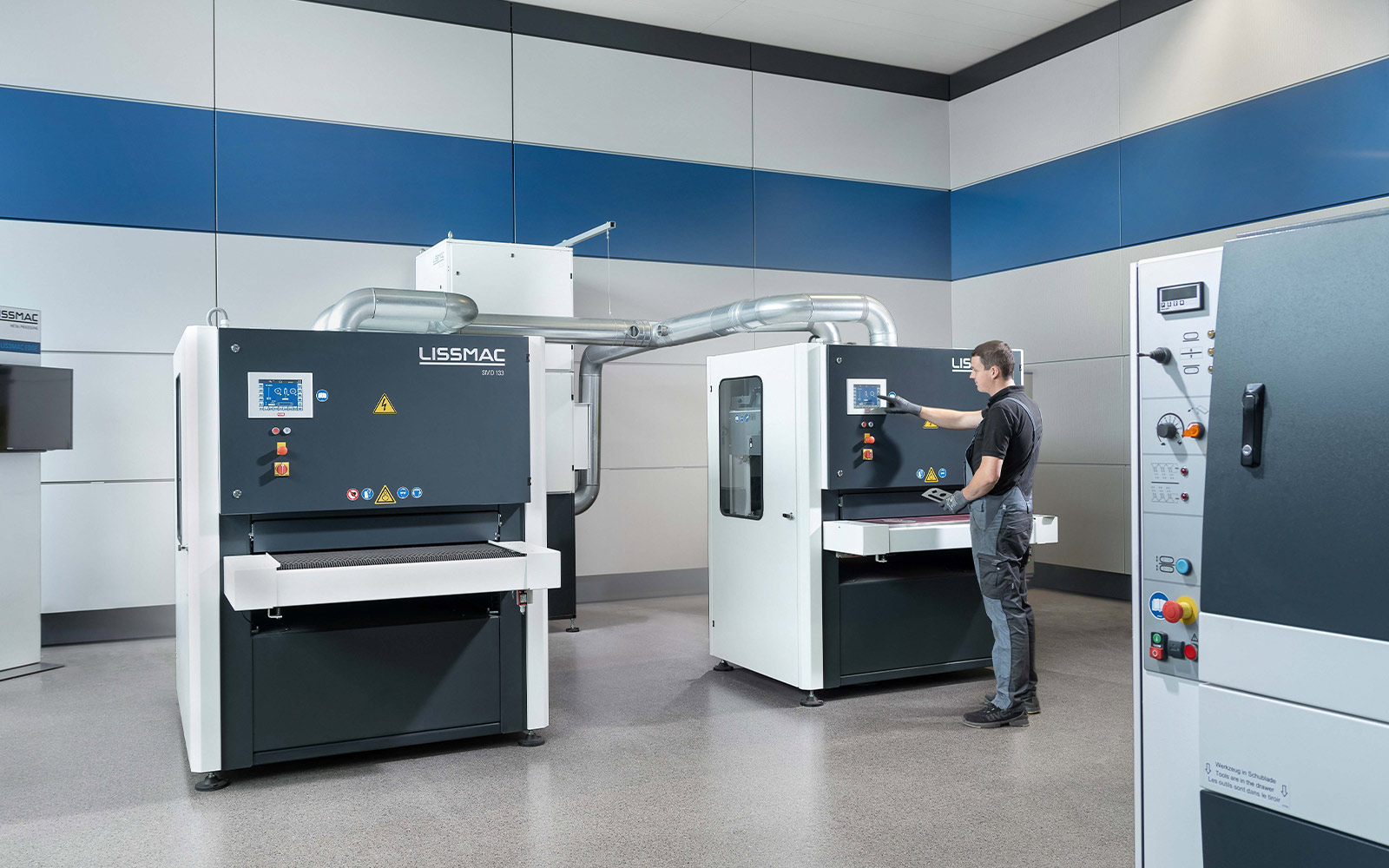
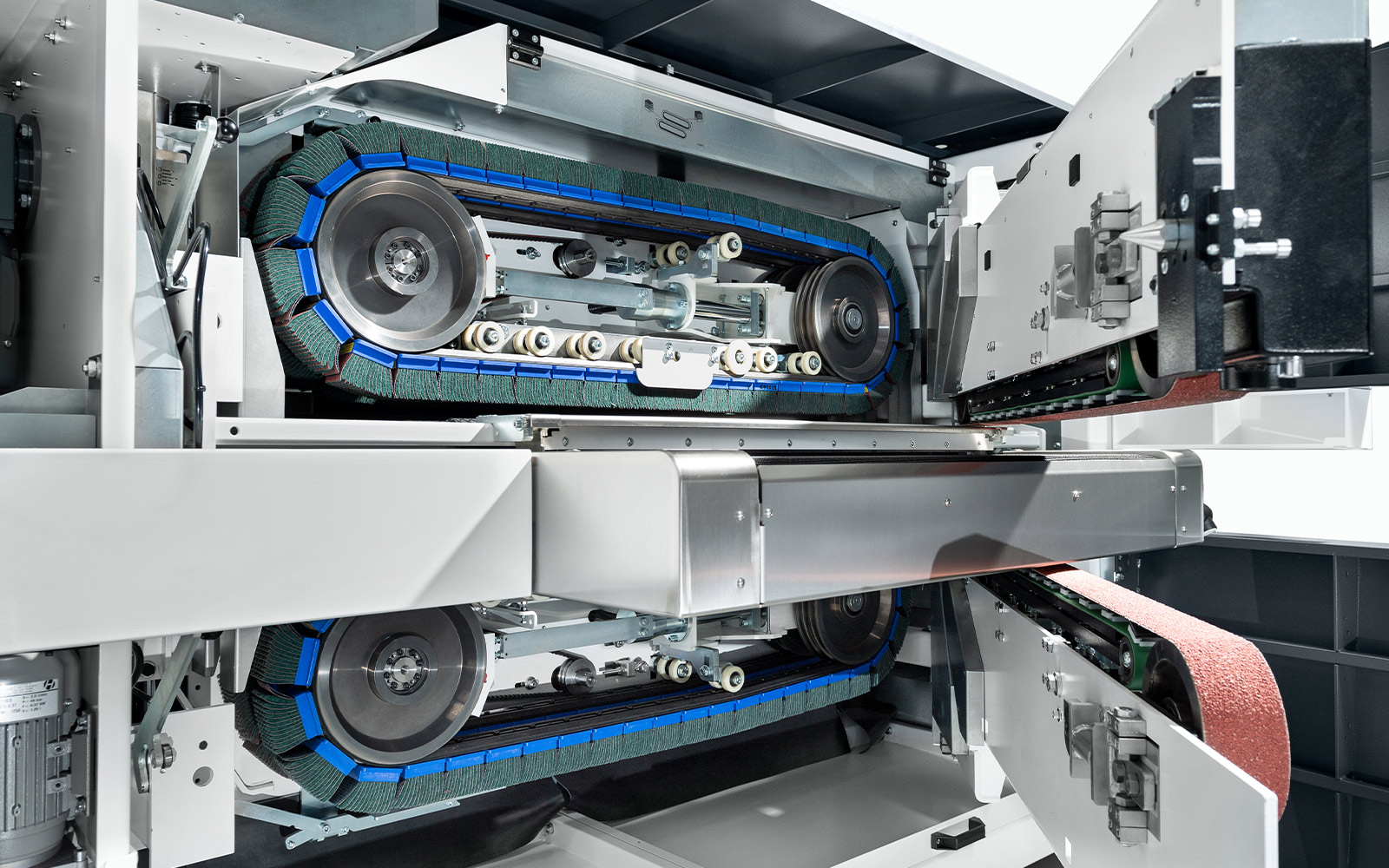
Innovative ideas to market leader - why LISSMAC is so successful
April 16, 2021
LISSMAC Maschinenbau GmbH from Bad Wurzach in Germany has been a solid player in international machine building for more than 40 years. In this interview, Robert Dimmler, Director of Sales for Metal Processing, speaks about the competences the firm provides.
Herr Dimmler, let’s get straight to the point: What are LISSMAC’s fields of competence and how have they been developed?
Our product and competence strong points lie firstly in building technology, our Construction Technology business area. That was the origin of the firm when it was founded in 1979. The Plant Engineering area emerged in the mid-80s. Work in this area began with special-purpose machines for the building materials industry and later came to include custom-tailored system solutions and turnkey projects for various sectors. These were LISSMAC’s only business fields of activity until the year 2000. There followed a diversification of the enterprise content and a stronger focus on industry. Today’s MT Handling branch emerged as a new field. Originally, handling systems with application-specific gripper solutions for all manner of industrial handling applications were developed and manufactured; today we mainly deliver solutions for the automotive industry. The youngest division is the Metal Processing branch. This is where steel brush, grinding and deburring machines for metal processing as individual and integrated complete solutions are manufactured. The Plant Engineering division now also focuses on the individual development and the economical automation of all manufacturing processes at LISSMAC and acts in task-based synergy with the other three fields.
Could you briefly outline the actual steps of development of the company and point out some highlights from each of the business areas?
In the summer of 1978, Siegfried Gebhart began work on the first ideas and design drawings for a stone cutting machine. Following successful series of tests with different stone systems, he decided it was time to begin series production, and with it to found a separate firm: LISSMAC was born. The newly founded LISSMAC then took out the patent for the stone cutting machine. The range of products was developed further, the business expanded and over the years, it became a company active worldwide. The building crisis of the 90s led to considerations of a broader positioning for the company.
The acquisition of MT Modern Technik GmbH & Co.KG offered the opportunity to enter into industrial handling technology. The subsidiary MT Handhabungs- und Robotersysteme GmbH was founded, and was integrated into the present-day MT Handling business area in 2009. The area was expanded successively over the years. Initially, most projects were small-scale. Today, over 90 percent of the volume is handling solutions for final assembly lines in the automotive industry, with far higher sales. We have built up extensive know-how in this field.
Another important milestone in the company’s development was the formation of the Metal Processing field. This field emerged out of a metal sheet production challenge for LISSMAC’s own manufacturing. The machining quality of laser-cut components needed significant improvement. We developed our own system concept for removal of the laser oxide layer, after which we quickly realised that there was demand for it outside our own company. Against this background, by 2003, LISSMAC had already brought a product out onto the market: the steel brush machine (SBM). The company’s new step forward then underwent intensive work by the Metal Processing field, which developed in a very dynamic way. One challenge still to be overcome, however, was surface machining. The acquisition of the metal division of Bütfering Schleiftechnik GmbH in 2012 with headquarters in Beckum provided a new opportunity. We could now offer freely configurable machines to our customers. As well as deburring, these systems enabled the creation of a specified surface grind in wet and dry processing. Beckum has since become LISSMAC’s second production site in Germany, as well as the service hub and demonstration centre for the north Germany region and Benelux. In 2018, LISSMAC took over the after-sales business for the metal grinding machines already on the market manufactured by Paul Ernst Maschinenfabrik GmbH, further developed selected technologies and meaningfully integrated these into the existing product portfolio.
In the Construction Technology field, our most lucrative division, I would like to mention the joint venture Nextec System AB with headquarters in Stockholm (Sweden), founded in 2017. This venture concerns a trenching process using diamond cutting technology to lay passive lines for fibre optic cable networking. As supplier of the trenching machines and the saw blades, we have recourse to technologies which we have mastered for years. We have expanded these technologies, optimised them and made them available for broadband networking.
You place special emphasis on the Metal Processing branch
This field plays a decisive role in the company. It brings in about a third of LISSMAC group’s total turnover. We started development of this business field practically from scratch. We then continuously expanded the product portfolio taking market requirements into account, and completed it with custom orders. I see LISSMAC as a market leader in this field. We can meet almost any customer requirement in the machining of thin and thick metal sheets with our products.
LISSMAC became increasingly active internationally in the 2000s.
For LISSMAC, these years were characterised by internationalisation. We originally focused on our core market in German-speaking countries. In the Metal Processing field in particular, we became increasingly active internationally, with our first international trade show at the EMO in Milan in 2003, and the following year at Euroblech. Customer interest was high, and so our international development began.
Our international sales activity was also expanded as a result. We are now active on over 40 international markets with sales and service, whether in our own right or through partners. Alongside the two sites in Germany, LISSMAC accelerated international activity by founding subsidiaries. Here, the subsidiary in the USA is of note, which takes care of sales and service for Metal Processing, but which also carries out small-scale local manufacturing. In 2019, LISSMAC USA was able move into a new building of its own. There is another subsidiary in China. It focuses on the manufacture of products for the building sector, such as standardised small-sized equipment. There are also subsidiaries in Dubai and Russia which serve the Arab and CIS countries.
Our export share also speaks for our internationalisation: 70 percent in the Metal Processing field and over 60 percent in the group as a whole.
What do customers value in the machine construction company LISSMAC?
Customers value the practice-oriented, innovative solutions and high level of quality of our products. We enjoy a high level of trust from our customers because we manufacture the systems ourselves. Since we have our own metal sheet manufacturing plant, we are familiar with the processes and challenges posed by production. Added to this is LISSMAC’s broad know-how in grinding and deburring technology, handling, conveyor technology and automation. Customers appreciate this, recognise the synergies at work and rest assured that we can act as solutions provider and systems supplier. And last but not least, honest communication is essential for us. What speaks most in our favour is when customers choose us again for the next system they purchase.
The service portfolio sounds very complex. How do you guide customers through this process?
Competent sales and an effective, flexible service network are, together with customised systems technology, the basis for successful collaboration. This begins with expert consulting in which priorities and customer requirements are defined and technical possibilities demonstrated. Sample processing of the customer’s workpieces in our application centres is a very important part of the process. Here, we can present all the solution approaches possible with the systems, and talk with the customers about the advantages and application limits in order, then, to work out what the best and most suitable solution is together. Our engineering allows us to implement customer-specific ideas which deviate from the standard. And after supplying the system, the after-sales field is, of course, decisive. We work with our own assemblers and qualified service partners. An effective service organisation is a critical factor when deciding to buy, since the customers participate in it over the whole service life of the machines.
Where will systems technology development take you now?
Various technologies are being further developed and adapted in the field of deburring technology. The machining of fibre-laser cut components plays an important part in this. Other aspects in focus are edge rounding up to radius 2 and a directionless finish, for which LISSMAC has developed its own solution with four rotor heads.
Industry 4.0 is on our agenda too. In particular, we are dealing with the integration of our technologies into existing manufacturing processes. For example, how can we integrate deburring technology into the existing material flow and process more efficiently? For example, by passing the pieces straight from cutting to the deburring machine and only then move on to sorting. We see great rationalisation and economisation potential for our customers.
Thank you very much for the interview.
Interviewer: Annedore Bose-Munde, Technical Journalist for Technology and Economy in Erfurt, www.bose-munde.de