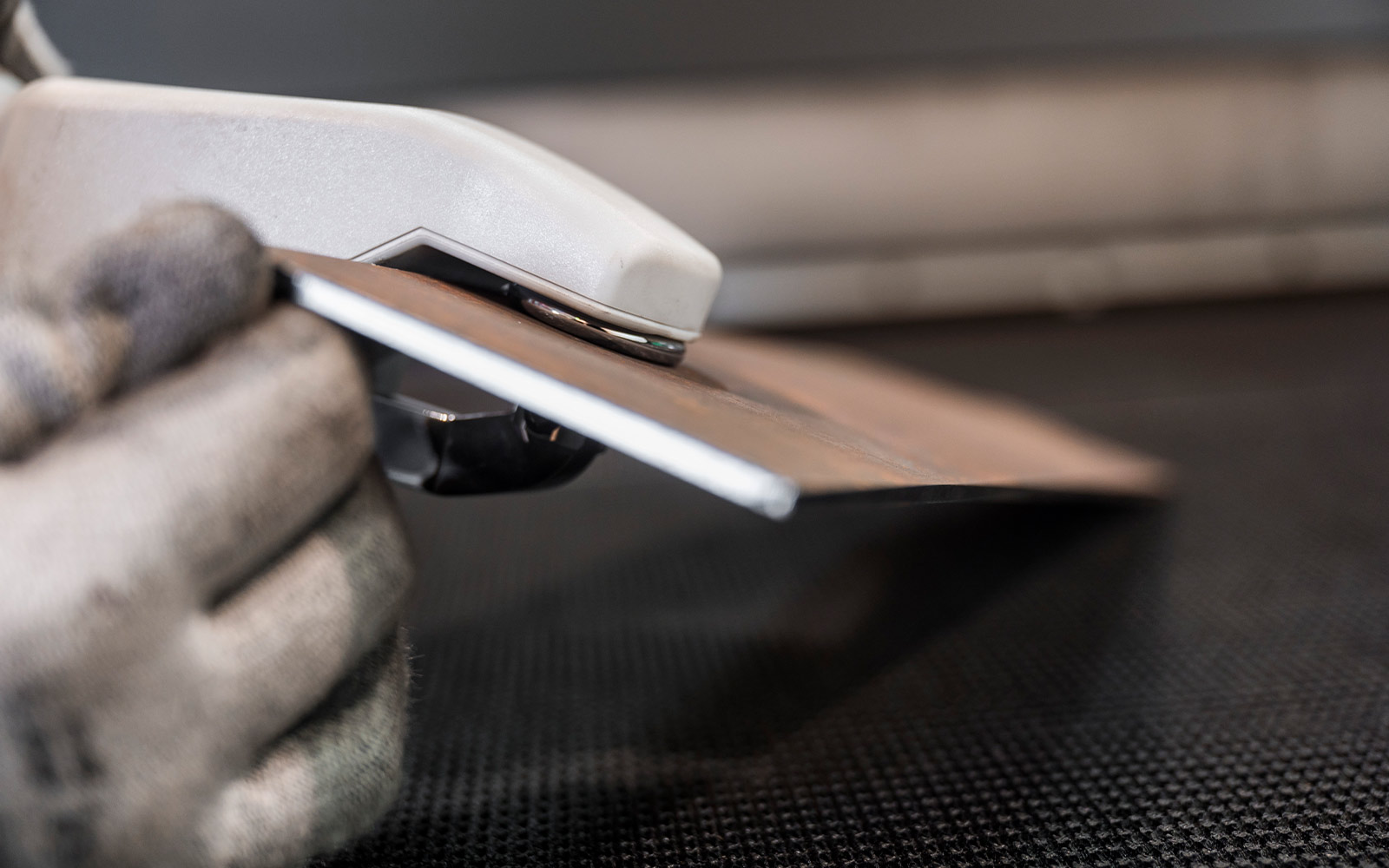
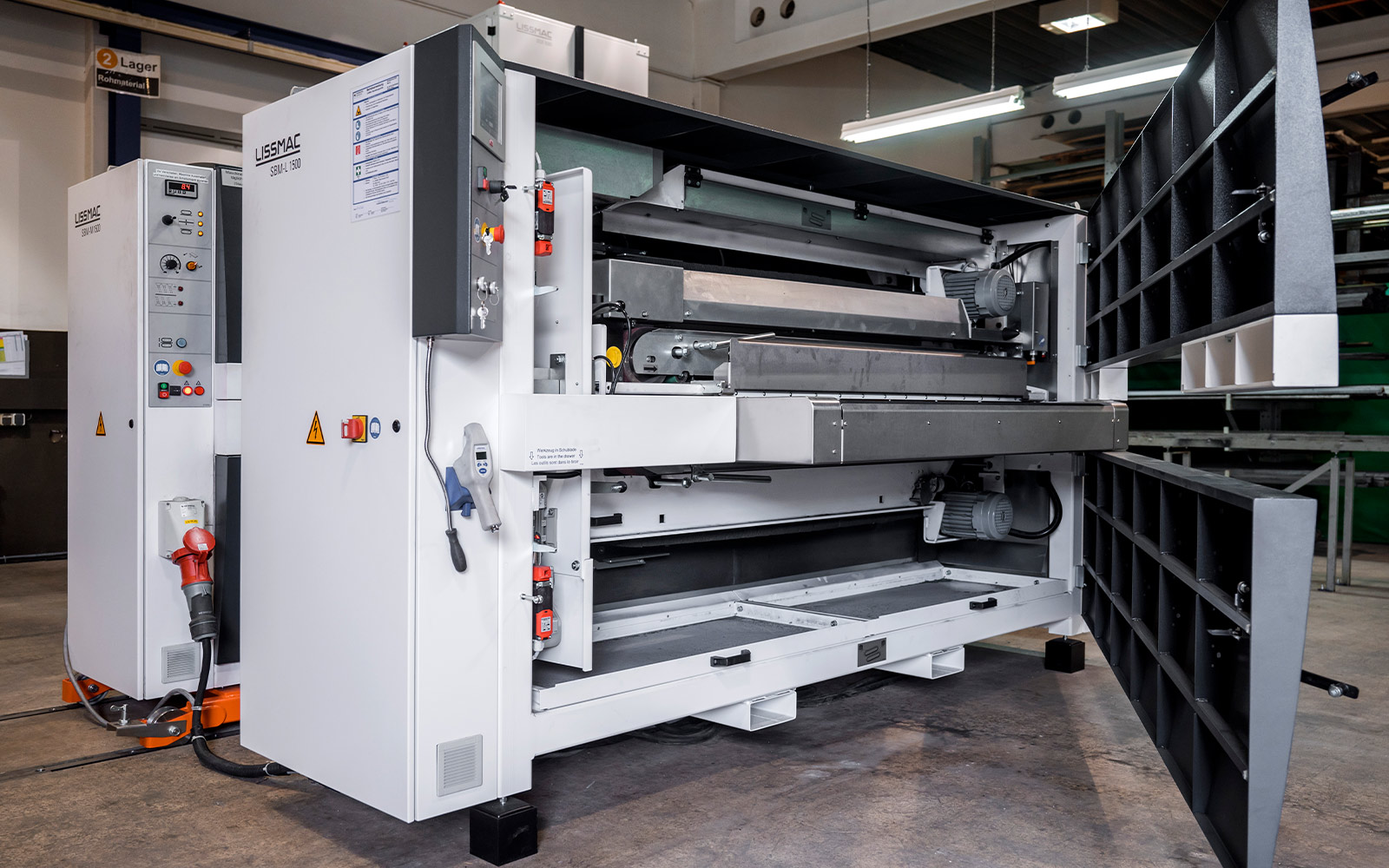
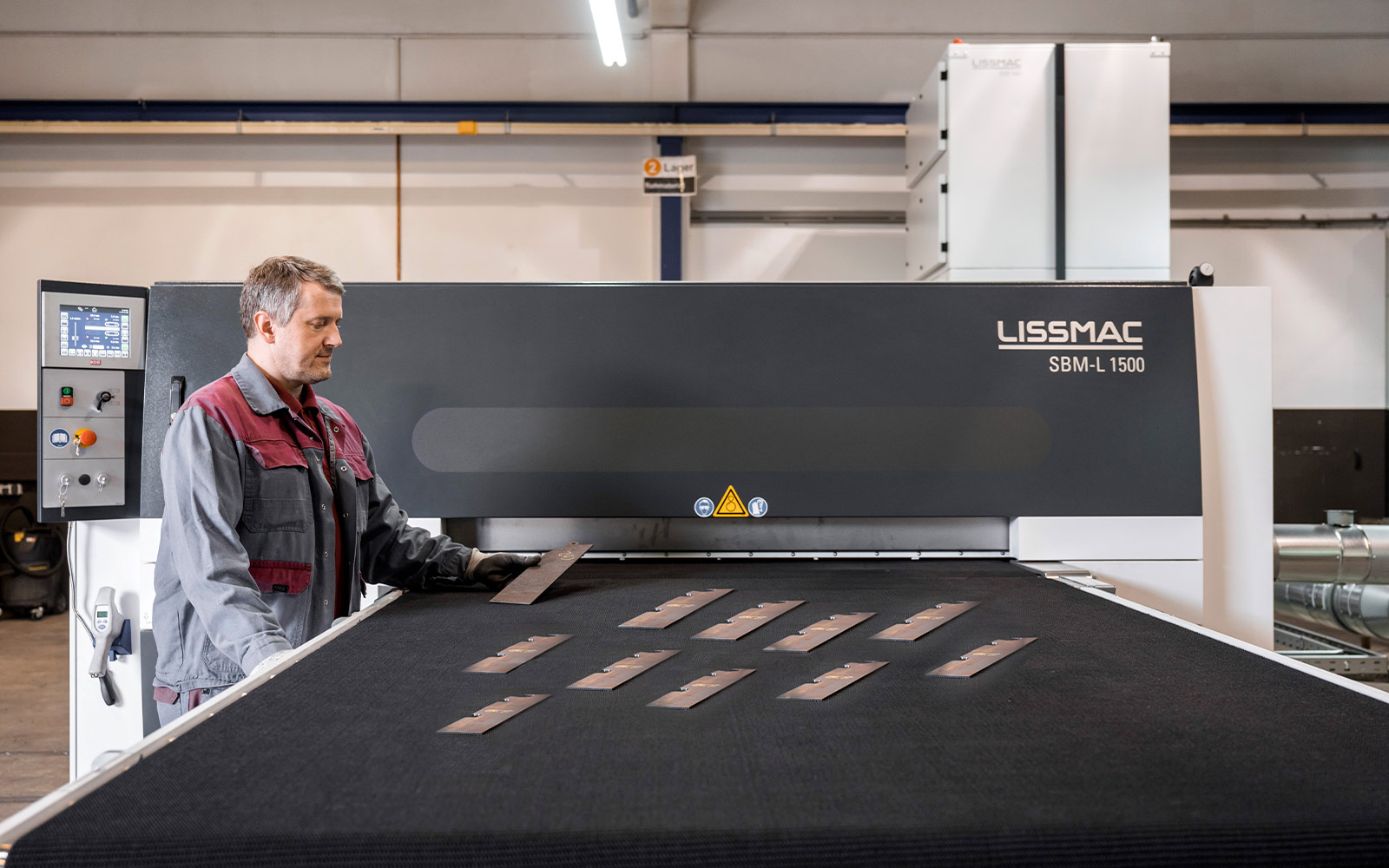
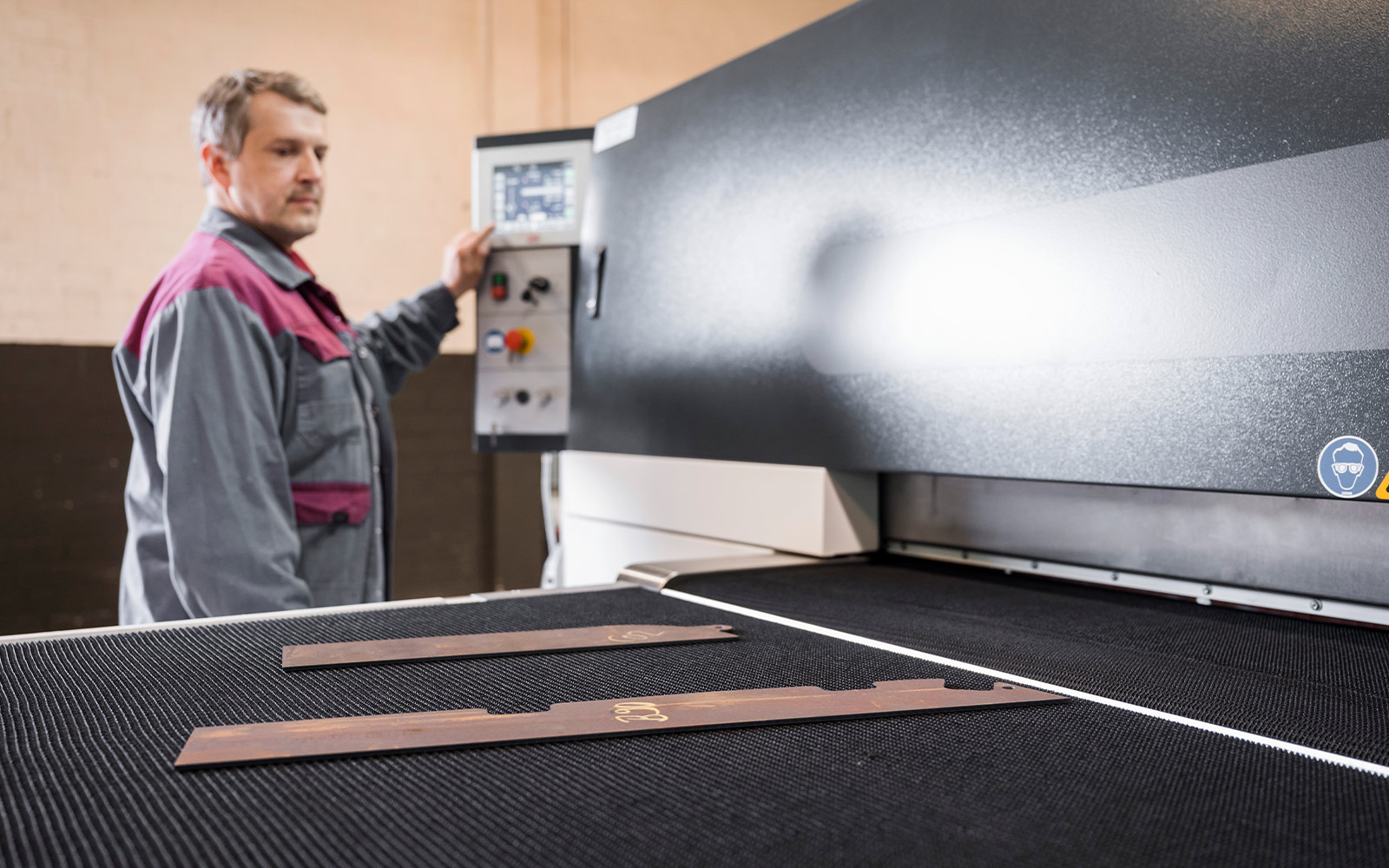
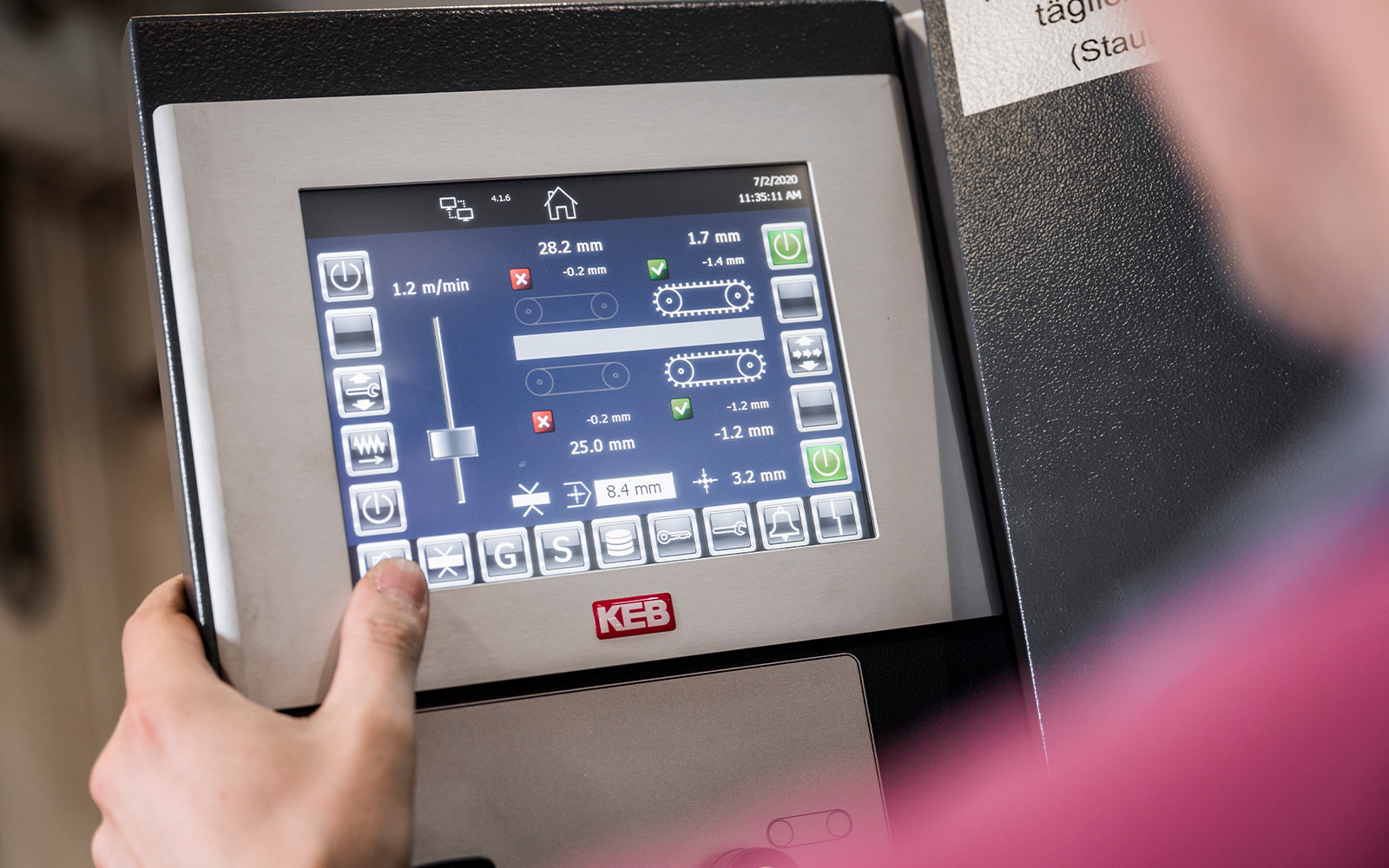
New grinding technology ensures quality and efficiency
Juli 01, 2021
New grinding technology ensures quality and efficiency in the production of special protection modules for security vehicles
Efficiency in production and quality are important parameters in sheet metal processing. That also includes, in particular, removing burrs from laser-cut parts before further processing or installation. In light of this, one manufacturer of security vehicles has invested in new, customised system technology.
At Farmingtons Automotive GmbH in Georgsmarienhütte, special protection solutions are manufactured for the automotive industry. For more than 40 years, the WELP Group, to which the company belongs, has acted as a specialist for the supply of safety productions to UN organisations (NGOs), authorities, VIPs, police, courts, banks and safety service providers throughout the world. The requirements and standards applied to the production and processing technology used for the components are accordingly high. Now the company has invested in a deburring brush line from LISSMAC Maschinenbau GmbH in Bad Wurzach.
Achieve higher quality and faster processes
“Due to the WELP Group’s new strategy alignment, it was also necessary to focus more on process efficiency and thus, process capacities, at the Georgsmarienhütte site. Another item is the increased alignment toward the OEM target group and the related quality requirements,” says Torsten Rieger, CEO of Farmingtons Automotive GmbH. For this reason, various challenges had to be overcome. For instance, with respect to corrosion protection, the coating quality should be increased to achieve further cost efficiency through faster processes. And work safety and working conditions should be improved. Therefore, the hunt for the right system technology was undertaken.
Gerold Hilger is responsible for production control at the company and, together with Leonid Muilar, was responsible for the project and the related new procurement. He brings complex expertise in the field of laser and brushing systems from previous activities. Thus, the idea of using a brushing machine arose.
“Farmingtons Automotive uses oxygen for laser cutting. This results in an oxide layer on the cutting edges where the coating can spall again. The sharp edges also pose an injury hazard. And, last but not least, the scale has to be removed from the armour steel processed in the special vehicles in Georgsmarienhütte,” Hilger summarises the situation. If possible, all three technical problems should be solved with the new system technology.
Processing the sharp laser edges
The initial contact with the machinery manufacturer, LISSMAC, was made in 2018. Together, the situation was analysed. The results were presented in a qualified manner after performing tests with components. On the basis of these basic parameters and the specifications from Farmingtons Automotive, LISSMAC developed a suitable machinery concept.
“The objective was to cover the highest possible degree of component diversity of the parts with the system technology. After all, approximately 1,500 different components made of a wide variety of materials and with a variety of thicknesses are manufactured in Georgsmarienhütte. In addition, the machine needed to remove the oxide layer in only one work step and round the edges on both the top and bottom,” says Thorsten Rieger.
“But, at that time, Farmingtons Automotive was already considering procuring a fibre laser. Fibre lasers in particular create cutting burrs. So, once again, comprehensive tests with sample parts were conducted and the results were evaluated. And, once again, various system concepts were created with a view to procuring the fibre laser,” Dirk Schürstedt, Regional Sales Manager for Metal Processing at LISSMAC Maschinenbau GmbH describes the decision-making process.
New system meets all requirements
In the middle of 2019, the decision was made to invest in LISSMAC technology. The LISSMAC SBM-M 1500 B2 steel brushing machine is located directly behind the SBM-L-G1S2 grinding machine which are linked both mechanically and with respect to their control technology.
With the grinding and deburring machine, which work with a dry process, both sides of parts made of steel and stainless steel can be processed, in alternating operation, in only one work step. It is designed for debrruing and evenly rounding the workpiece edges on the exterior and interior contours. The steel brushing machine also works with a dry process. Four brush belt units with two tilted brushes each on the top and bottom, working in opposite directions, ensure optimal cutting edge processing. The sheet metal parts to be processed automatically run through the machine. The four brush belt units brush off the oxide layers on all interior and exterior edges. Thus, in only one work step, edges and surfaces that are suitable for coating are created on both sides. In addition, process safety is ensured by means of an automatic thickness measurement.
The new system also scores points with respect to working conditions. The dry dust extractor allows for the exhaust air to be recirculated into the room with a degree of purity of 99.9 percent.
Significant savings potential achieved
Farmingtons Automotive is very satisfied with the results achieved with the LISSMAC machines. Today, parts from one to fifteen millimetres and materials from construction steel to armour steel are processed with the new system technology.
“Almost 80 percent of the components can now be processed with the new system technology. Thus with respect to the processed spectrum of parts, only nine grinding hours per week are required in comparison with the thirty hours required to date,” says Peter Schulte, Production manager automotive engineering. In this context, the personnel costs for the process were significantly reduced. Since the machine also removes the scale, the costs for cleaning are also saved.
And employee satisfaction has also increased. Due to the new system, it is no longer necessary to work in the grinding cabin or wear hearing protection and a mask. The employees are now better protected due to the dust filters in the system.
The company has now also become more flexible with respect to the production of new company. Now, both large and small components can be processed as can various thicknesses and materials. This is a great basis for being prepared for future trends and requirements.
Last but not least, the important topic of quality is covered. The components manufactured in Georgsmarienhütte are primarily considered special protection modules for all-terrain vehicles, pick-ups and vans and are screwed into the vehicles later. Depending on the customer’s wishes with respect to equipment and on the specific vehicle, that amounts to between 40 and 70 components per vehicle. These so-called component kits are safety certified and therefore have to meet the highest quality requirements and, accordingly, have to be precisely manufactured. Service life documentation is indispensable for these types of vehicles because, ultimately, they are used to protect human life.
The production area in Georgsmarienhütte was expanded by 6,000 m² at the end of 2020. However, Peter Schulte is already thinking about the next efficiency topic in this context: “The long-term plan is to introduce an automation system between the laser and the deburring brush machine.” The potential addition of a system for barrel finishing the smaller parts is also being discussed. So, Farmingtons Automotive is very well-prepared for the future.
Text: Annedore Bose-Munde
Images: WELP Holding GmbH